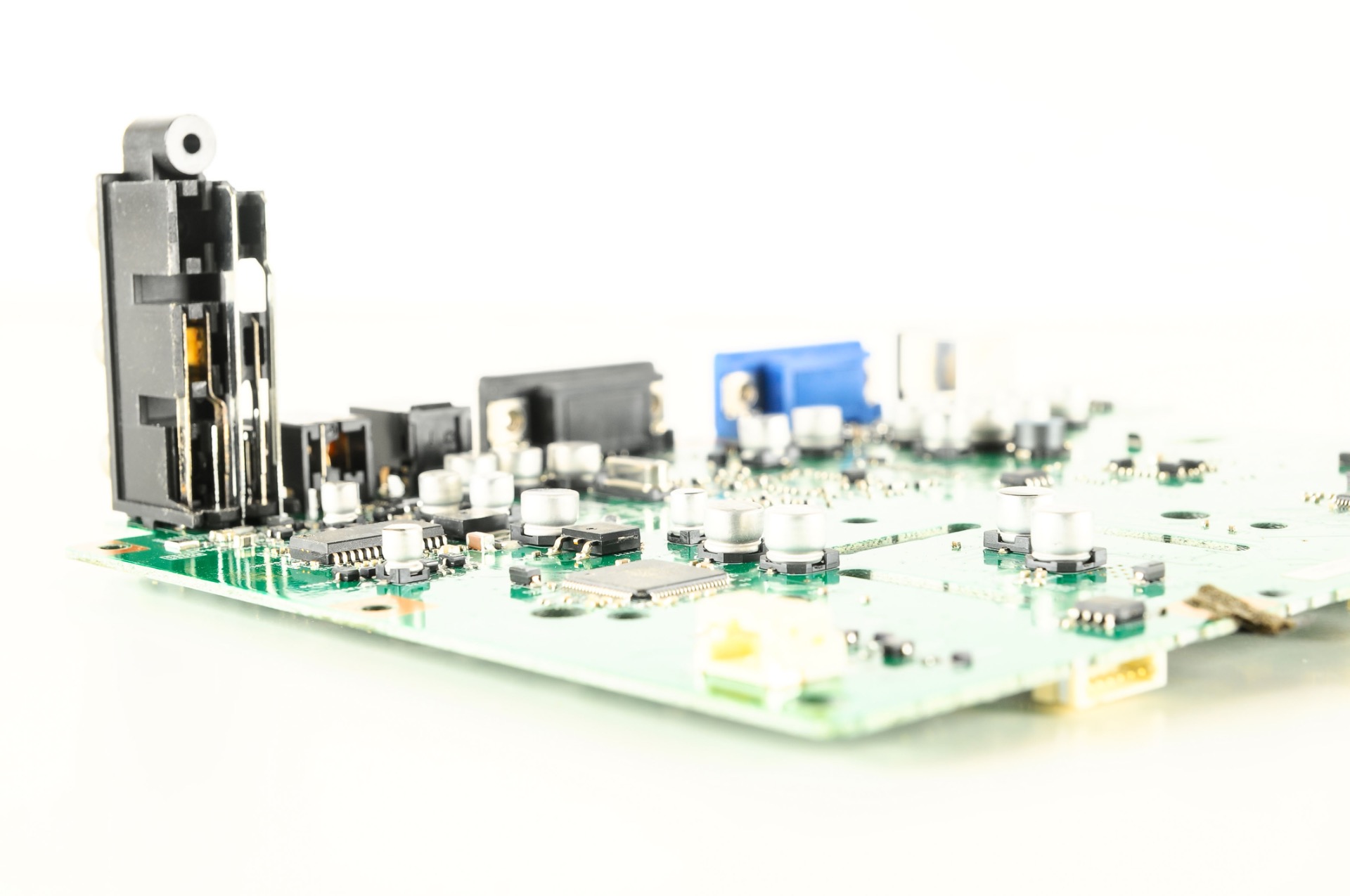
Crimp Contact-Based PCB Connectors vs. IDC Socket Connectors
Introduction
In PCB connectivity, engineers and designers often choose between crimp contact-based PCB connectors and IDC (Insulation Displacement Contact) socket connectors. Each type offers unique advantages and limitations depending on the application. This blog post will explore the pros and cons of both, as well as the most common brands that supply these connectors.
IDC Socket Connectors
IDC socket connectors are insulation displacement connectors that allow automated termination without the need for crimping individual contacts. They are widely used in ribbon cable applications, computer interfaces, and industrial control systems.
Pros of IDC Socket Connectors
Fast and Automated Assembly – IDC connectors enable quick mass termination of multiple wires, reducing labor and improving consistency.
Reliable Connections – The insulation displacement blades pierce wire insulation to create a solid electrical connection, minimizing contact resistance.
Cost-Effective in Large Scale Production – The mass termination process saves on assembly costs for high-volume production.
Ease of Use – IDC connectors are easy to install and do not require stripping or crimping, making them convenient for assembly lines.
Good for Flat Ribbon Cable Applications – Ideal for data transfer and control applications using flat cables.
Cons of IDC Socket Connectors
Not as Secure Under Vibration – IDC connectors rely on insulation displacement rather than mechanical crimping, making them more prone to failures in high-vibration environments.
Limited Flexibility – IDC connectors are designed for specific wire types and cannot accommodate a broad range of wire sizes like crimp-based connectors.
Higher Risk of Contact Wear Over Time – The insulation displacement blades can weaken over repeated mating cycles, leading to connection failures.
Common IDC Socket Connector Brands
TE Connectivity – Offers IDC socket connectors for industrial and computer interface applications.
Molex – Provides reliable IDC connectors for ribbon cables and PCB mounting.
3M – Specializes in IDC ribbon cable connectors for data and control applications.
PCB Connectors with Crimp Contact Terminals
Crimp contact-based PCB connectors use individually crimped terminals inserted into housings, offering a traditional and widely used method of electrical connections in PCB-mounted applications.
Pros of Crimp Contact-Based PCB Connectors
Tighter and More Secure Connectivity – Crimp contacts are mechanically locked into housings, ensuring excellent vibration resistance and long-term stability.
Greater Customization – Engineers can select specific wire lengths, configurations, and contact plating based on application needs.
High Mechanical Strength – The crimping process ensures a robust physical connection that withstands tension and movement.
Modular Design – These connectors allow for easy integration and flexibility in PCB layouts.
Good for Low-Volume and Prototyping – Unlike IDC, crimping can be done manually with hand tools, making it suitable for prototyping and small-batch production.
Interchangeability – Many crimp contact PCB connectors follow standardized footprints, enabling easy replacements and repairs.
Cons of Crimp Contact-Based PCB Connectors
Time-Consuming Assembly – Each wire must be crimped and inserted individually, increasing assembly time compared to IDC connectors.
Manual Labor Dependence – While automated crimping machines exist, many applications still rely on manual crimping, which can introduce inconsistencies.
Higher Risk of Assembly Errors – Incorrect crimping or loose contacts can result in connection failures and require additional quality control measures.
Common PCB Connector Brands with Crimp Contact Terminals
TE Connectivity (AMP, Deutsch) – Offers a broad range of crimp connectors, from PCB-mounted options to automotive and industrial-grade solutions.
Molex – Provides widely used crimp contact PCB connectors like Micro-Fit, Mini-Fit, and Mega-Fit series.
Amphenol – Supplies high-performance PCB connectors with crimp terminals for aerospace, industrial, and telecommunications applications.
Wire Harness Considerations
When designing and manufacturing wire harnesses based on these connectors, several key points must be considered to ensure reliability and efficiency:
Connection Stability – Crimp contact-based connectors provide superior mechanical strength and should be preferred for applications subjected to vibration and mechanical stress.
Assembly Process Control – Crimping requires precise force and calibration to prevent poor connections, while IDC connectors require consistent wire insertion depth.
Harness Routing & Strain Relief – Proper cable routing and strain relief techniques must be used to prevent excessive bending or stress on IDC and crimp connections.
Quality Assurance & Testing – Electrical continuity testing, pull-force tests, and visual inspections should be implemented to verify the integrity of each connection.
Production Volume & Cost Efficiency – IDC connectors are ideal for high-volume production with automated termination, whereas crimp contact connectors provide more flexibility for low-volume and customized applications.
Repair & Maintenance – Crimp contact connectors allow for easier repair and replacement, whereas IDC connections are often permanent and may require complete replacement if damaged.
Which One to Choose?
The choice between crimp contact-based PCB connectors and IDC socket connectors depends on several factors:
For Fast, Automated Mass Termination → IDC connectors offer rapid wire termination without the need for individual crimps.
For High-Vibration Environments → Crimp contact connectors provide mechanically locked connections that prevent loosening under stress.
For Long-Term Reliability → Crimp connections are more durable over multiple mating cycles compared to IDC connectors.
For Modular and Customizable Designs → Crimp connectors offer flexibility in wire selection, configurations, and layouts.
For Space-Saving Ribbon Cable Applications → IDC connectors work well for compact and high-density wiring solutions.
Conclusion
Both crimp contact-based PCB connectors and IDC socket connectors serve essential roles in PCB applications, each with distinct advantages. While IDC connectors shine in fast, high-volume automated termination, crimp contact-based PCB connectors offer superior mechanical stability, long-term durability, and customization. From a wire harness manufacturing perspective, factors such as vibration resistance, ease of assembly, testing procedures, and repairability should be carefully evaluated to select the best solution for the application.